PTFE - this shortcut stands for polytetrafluoroethylene, the high-tech plastic of superlatives.
What you should know about PTFE and why it is a material for specialists
Polytetrafluoroethylene (PTFE) is a linear polymer composed of fluorine and hydrocarbon. As a semi-crystalline fluoroplastic with the highest degree of fluorination, PTFE has a molecular structure in which there is an extremely strong bond between the carbon and fluorine atoms. The fluorine atoms shield the carbon chain almost completely. This structure results in a unique combination of valuable usage properties.
The high-performance plastic polytetrafluoroethylene has the highest resistance to chemicals and the lowest coefficient of friction of all comparable plastics. In addition, there are first-class thermal properties, because PTFE is stable in a wide temperature range. Because fluorine is the most electronegative element, the polymer PTFE also has excellent dielectric properties. Its high pureness and longevity are further advantages of this remarkable material.
Due to the unique combination of the best usage properties, PTFE is now the most commonly used fluoroplastic in many industries, better known under trade names such as Teflon®, Dyneon TM, Fluon® or Gore-Tex®.
Some characteristics that distinguish polytetrafluoroethylene as a particularly high-quality polymer have already been mentioned. In addition, this material has a number of other remarkable properties.
The heat resistant in a temperature range from -200 to +260 degrees Celsius has to be emphasized, whereby PTFE is resistant even in continuous operation at temperatures from -200 to +250 degrees Celsius. The substance remains insoluble even when heated shortly to more than 300 degrees Celsius.
Due to its inertness, polytetrafluoroethylene is insensitive to almost all chemicals. Even aggressive acids cannot harm the material. The polymer is also resistant to substances used in the production process, such as alcohol, petrol, oil, etc. PTFE is just as robust against weathering influences (such as frost, UV radiation or wetness). The impact of ozone or oxygen is also harmless to the material.
PTFE does not absorb water, but rejects it. It is also insensitive to water steam. The material decomposes in contact with open fire, the flames erase by themselves.
The excellent sliding properties of the material create a self-lubricating effect. At the same time, the coefficient of friction of polytetrafluoroethylene is extremely low. Since static and sliding friction are the same size, the passing from standstill to movement is smooth, so there is no stick-slip effect. The extremely low surface tension means that no other material sticks to polytetrafluoroethylene.
PTFE has extremely low dielectric properties paired with a high surface- and specific volume resistance.
The material is also characterized by a high elongation at break and a high flexural fatigue strength.
Not to forget: PTFE is physiologically harmless, that´s why it is perfect for use
in the food industry.
Special procedures for plastics processing (plastics compounding) can be used additionally to modify the material properties for specific requirements. If Is polytetrafluoroethylene is mixed with organic or inorganic substances like graphite, glass fibers or metal powder, product properties such as hardness, abrasion or pressure resistance can be further improved.
Thanks to its excellent properties, polytetrafluoroethylene fulfills the highest technical requirements and is suitable for a wide range of uses in a wide variety of industries. The material has proven itself many times in practical use as a coating, sealing or sliding material, as well as for highly stressed components and in particularly sensitive production processes, and has become the most commonly used fluoroplastic by the industry.
Industries which use PTFE:
Chemical industry
Electrical engineering and semiconductor industry
Pharmaceutical Industry
Medical technology and medical device construction
Transport and conveyor technology
Textile industry
Consumer goods production
Biotechnology
In everyday life we encounter numerous products that owe their special usage properties to the use of PTFE.
Non-stick coatings made of polytetrafluoroethylene on pans and pots prevent ingredients from sticking during roasting and cooking.
Lenses coated with polytetrafluoroethylene do not get dirty so quickly and are easier to clean.
By using wafer-thin PTFE films, the textile industry produces breathable, water-repellent textiles that, for example are offered under the brand name Gore-Tex®.
In addition, polytetrafluoroethylene is used in many fields across all industries
The unique combination of positive usage properties offers a very wide field of applications for the raw material. Therefore, this material could also be of interest to companies in the future who don´t know and don´t use it yet.
PTFE – alternative material for many production areas
As a special plastic with excellent usage properties, PTFE is already being used successfully in many industries. When it comes to sophisticated system solutions in technical applications, the choice will probably fall more often on PTFE in the future.
It can be observed that polytetrafluoroethylene is often an alternative to previously used materials. Not only in terms of its properties, but also in terms of economy and cost efficiency, this thermoplastic is clearly superior to various conventional materials. Even if the corresponding component or semi-finished product is possibly a little more expensive to buy, its longevity always makes up for it. In the longer term, the use of PTFE almost always proves to be a cheaper alternative. Long service lives guarantee excellent functionality, offer more security and reduce maintenance efforts. Particularly in critical applications, the use of this material results in solid competitive advantages.
Application examples from different industries
In the construction industry, coatings made of PTFE are used to protect surfaces (facades, roofs, etc.) from the weather.
Its chemical inertness and the associated resistance to almost all chemicals make polytetrafluoroethylene a wanted material in the chemical industry, for example for the lining of pipelines in chemical plant construction.
In electrical engineering as well as in its special areas of high voltage and high frequency technology, PTFE is used as an electrical insulator (e.g. insulation material for cables) due to its high dielectric strength and partial discharge resistance. Because of its low dielectric constant the raw material is also suitable for the production of high-frequency printed circuit boards.
The excellent sliding properties of polytetrafluoroethylene are used in the construction of bridge bearings as well as for seals under dry running conditions.
Due to the extremely smooth, liquid-repellent surface of the material, the long service life and its excellent physiological tolerance, polytetrafluoroethylene is ideal for the manufacture of vascular prostheses (stents and bypasses) as well as implants in plastic surgery. When inserting dental implants, a membrane made of PTFE can support bone build-up and controlled tissue regeneration.
The fact that PTFE can be steam-sterilized at temperatures above 100 degrees Celsius without damage also proves to be an advantage in medical and laboratory technology.
The overview of the diverse application areas of PTFE clearly illustrates how the first-class properties of this technical material are used in various industries. For two selected branches of industry, in which polytetrafluoroethylene plastic is used particularly often, the following is an example of how diverse are the possible uses.
High functionality in mechanical engineering
In mechanical and plant engineering, PTFE is a preferred material due to its unique property profile. In all production areas in which components or semi-finished products are required, which are subjected to high mechanical stress, but are simultaneously as wear-resistant as possible, polytetrafluoroethylene is perfect.
Semi-finished products made of PTFE (such as plates, round and hollow bars, pipes, etc.) can be easily processed into dimensionally stable, precise components by using cutting technology. Components and construction parts made from the material are characterized by longevity and high strength and are almost maintenance-free.
For example, Casings and coatings made of PTFE protect pistons and rollers from corrosion and early wear. Films, hoses, adhesive- and sealing tapes, which are offered as semi-finished products, are used here in particular.
Due to its low frictional resistance, PTFE is also suitable as a solid lubricant.
For special applications mixtures of polytetrafluorethylene can be prepared by the addition of selected additives that are precisely tailored to the intended use.
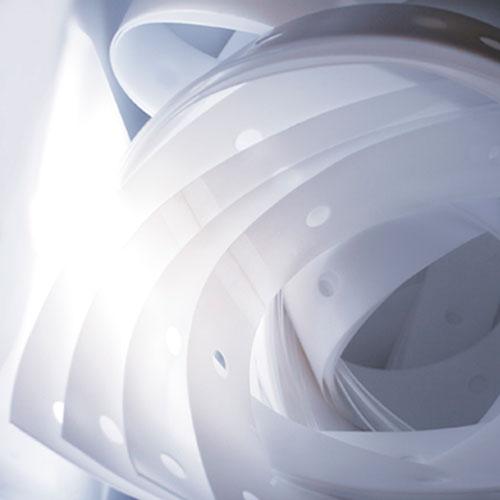
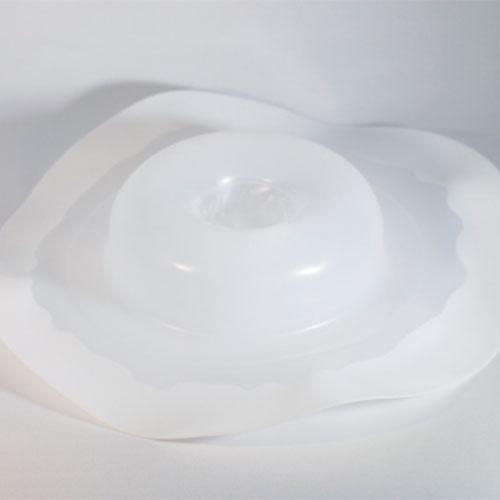
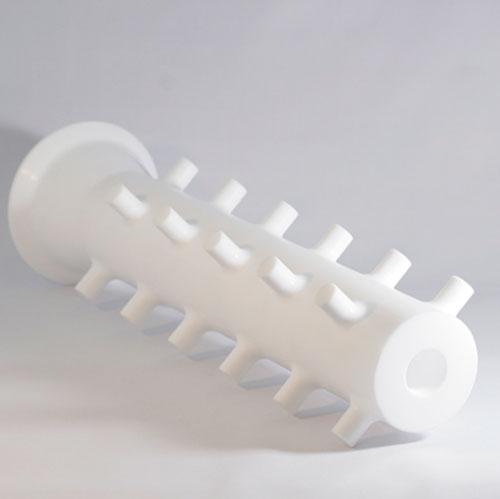